As Carbon reduction continues to become a central focus for North American food producers refrigeration waste heat is a key strategy to get there.
For most food producers, refrigeration is mission crucial to producing and storing food throughout production. It is common knowledge that refrigeration systems generate considerable quantities of heat. Traditionally, refrigeration and cooling systems have been viewed as separate to the heating systems that are installed within the same facility or site. To get to Net Zero realistically plants will be required to look a the total thermal system as one complete system.
As you are looking to incorporate waste heat into your plant, here are a few areas that you could start with:
Boiler or Direct Water Heater Replacement
A boiler or direct water heater generates most heat within Industrial food processes. For most food production facilities applying heat at one or more stages is common in eliminating microbiological risk, cooking food, sanitation of pre-filling stage, pasteurization or sterilization of packaged food, cleaning and sanitation procedures of equipment’s surfaces. Boilers often use natural gas as a primary fuel source and by using the waste heat from the refrigeration system can reduce or eliminate this source of greenhouse gas.
Wash Down Water Production
Food processing equipment can get dirty during production, and even a miniscule amount of waste can leave a biofilm that pathogens could lead to colonizing of pathogens. Waste heat from the refrigeration system could be used to pre-heat hot water for this application.
Process and Production Heating
Process and Production heating is crucial in maintaining perishable food items that require very specific temperature, humidity and ventilation conditions. Process heating systems may rely on numerous methods for generating and moving heat that generate carbon emissions through fuel, electric, and steam systems. When it comes to using waste heat usage within could include preheating water, pre-treating in-coming fresh air, and space heating or cooling.
Getting started
If you think that this may fit into your climate reduction plan the first step is to determine if the refrigeration and the heating demands are required at the same time. This will determine if you will require thermal storage in the form of an ice battery or water tank. Next, you will want to note the amount of temperature, frequency, and amount that you require to understand your demand requirements. Once this is determined, a refrigeration contractor such as CIMCO can help you determine your best solution to tie into the refrigeration system.
When it comes to retrofitting and opening up to using waste heat, its all about taking the first step, even by offsetting a small amount of energy or emissions will provide a displacement of fossil fuels, reduction of energy, and a reduction of carbon emissions.
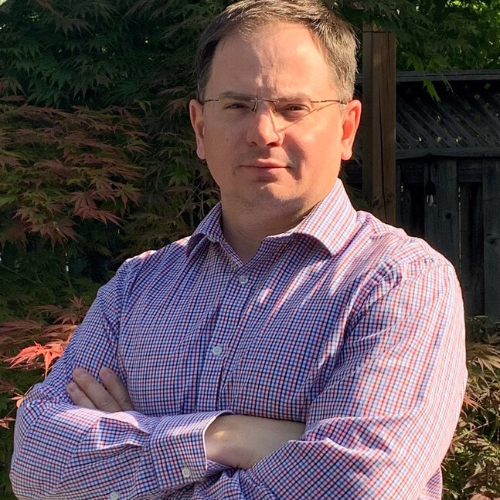
Jonathan Berney P.Eng - Business Development Manager for Ontario
With more than 16 years of refrigeration experience in cold storage, food & beverage and recreational markets, Jonathan has broad exposure to natural refrigeration and new technologies and is involved in all aspects of refrigeration projects from initial design concept to project execution and install.
Related Posts
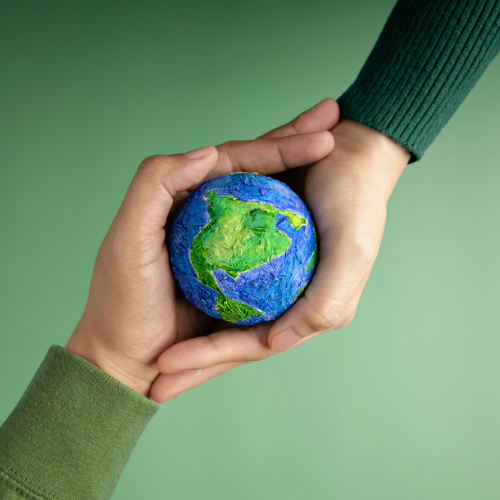
Navigating HFC Regulations: Federal and State Initiatives to Reduce Global Warming Potential
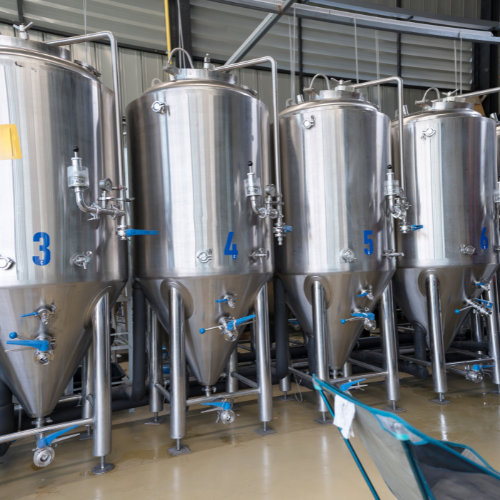
Decarbonizing Food Processes with Industrial Heat Pumps
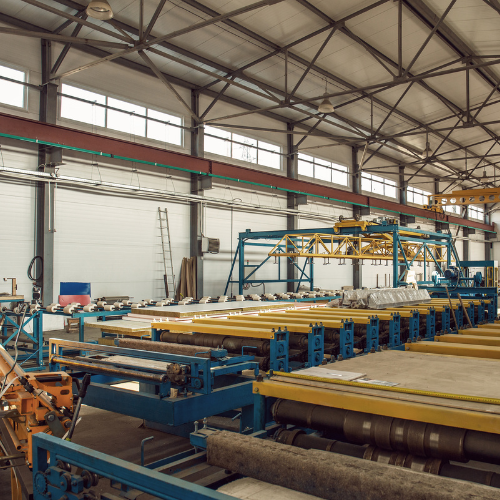
Interconnected Efficiency: Leveraging Ammonia Heat Pumps for Sustainable Manufacturing
STAY UP TO DATE
Get the latest industry insights and important updates delivered right to your inbox.
|