Recently, a valued customer of CIMCO, a poultry processing plant located in the U.S. state of Georgia, ran into an unexpected issue with the breakdown of an evaporative condenser. This resulted in one of the facility’s two production lines going down – a significant disruption to operations.
It was of utmost importance to get the facility fully operational again as quickly as possible to minimize downtime. However, getting a new condenser of that size could take up to six months to deliver and install, resulting in ongoing financial losses for the facility.
CIMCO has strong representation across all of North America, allowing for rapid and responsive action during emergency situations like these. At the time of the condenser breakdown, CIMCO was already working on a project for the same customer in Louisiana, where a new condenser was on-site but didn't have an immediate installation deadline. This allowed the team to act quickly and take advantage of a bright idea the customer had, which involved moving the condenser from Louisiana to Georgia.
The CIMCO team accepted the challenge and pulled out all the stops to get the facility back online in record time. In less than two weeks total, the breakdown was fixed and both production lines were seamlessly running at full speed again.
A Tight Deadline
The breakdown happened on a Tuesday, only a week before the September Labor Day long weekend in the U.S. This meant that some places were closed over the weekend, and acquiring the parts and permits needed became a challenge in itself. However, the team was determined to make a viable plan and get the customer fully operational again.
The following Monday, a representative was dispatched to the site to gather insight into what exactly would be needed. Between Tuesday and Friday, the team devised the plan and executed all the subcontracts. This involved collective coordination of all departments, including the arrangement of a crane and ancillary essentials to start the installation on Friday.
By Monday morning, on Labor Day, the evaporative condenser was up and running – fully installed and commissioned by the evening. As the customer requested, the plant was ready for its first poultry processing run again on Tuesday morning, exactly on time.
Overcoming the Obstacles
It wasn’t just a matter of relocating the equipment to a new site. There were countless planned and unplanned challenges that the CIMCO team had to deal with. As the site is located very close to an airport, it made getting in and out more difficult and required additional permits.
For instance, a 550-ton crane was needed to hoist the equipment into place, an operation for which a specialized permit was needed. Usually, this special permit takes 45 days to get. The team managed to work with the customer to get it within 24 hours.
Another pressing challenge was maneuvering the crane within the limits of the tight space on site and overhead power lines. Once the crane was in place, the removal of the old condenser (and disposing of it on such short notice) proved more complicated than anticipated. Providing steel structure reinforcements to accommodate the new, heavier, condenser was also imperative to facilitate the replacement.
CIMCO needed significant manpower to pull the project off in the allotted time. This meant a significant number of contractors were needed on site and successfully coordinating all the services in such a small space was very important
Thanks to the experience, skill, and dedication of the CIMCO team, the condenser replacement proceeded as planned and without incident.
“It all worked out, even though it was down to the wire,” said Chris Barker, Industrial Senior Project Manager – U.S. at CIMCO, who managed the project. “The customer was very happy with the end result.”
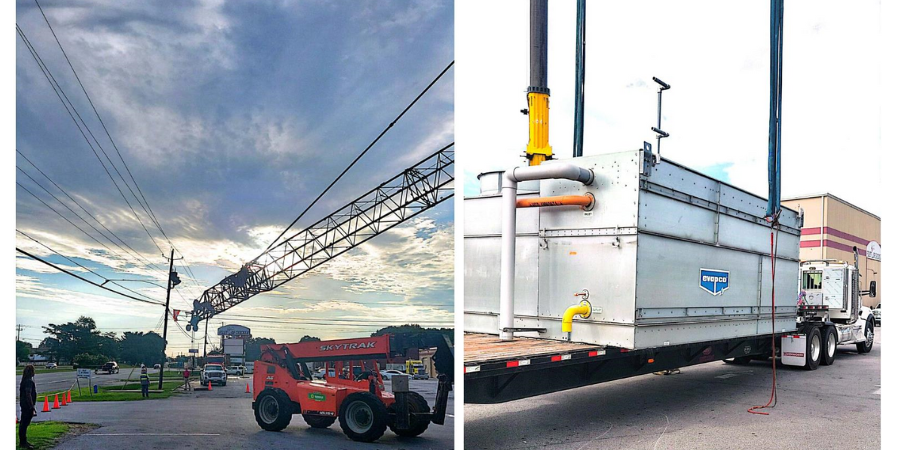
Thank You to the Team
“I was not only impressed by everyone’s work ethic but the great attitudes they had throughout,” said Barker. “It really made me proud to be part of the CIMCO team.”
A special word of thanks goes out to the following people:
- Steven Sawyer was the foreman on site and did a fantastic job keeping everybody on track, on schedule, and fully informed of the progress.
- Fred Lewis was the service technician and was instrumental in the success of the project, working over the holiday weekend to find the last missing pieces needed.
- Doug Johnson was the general superintendent who worked closely with Barker to pick out the material list and find the manpower needed.
- David Yeager was the salesman who went to the site to collect all the information and work with the team to develop the overall plan.
- Jeffrey Hinson was the Vice President who had an exceptional relationship with the customer and the confidence that the CIMCO team could execute this work in time.
- Tyler Schingle was the engineer who worked quickly to make sure the plan would not only work but was also in compliance with the required codes.
“Everybody did their job to the best they could – and beyond,” concluded Barker.
Related Posts
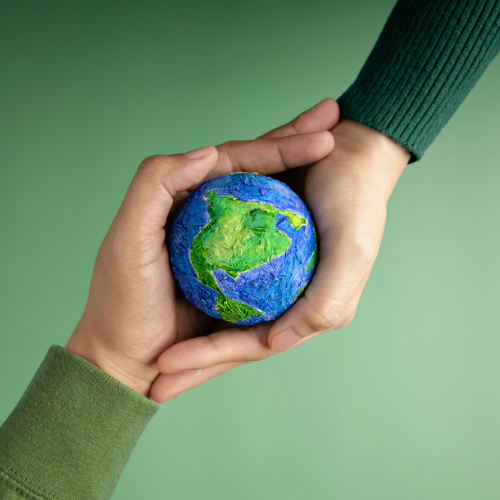
Navigating HFC Regulations: Federal and State Initiatives to Reduce Global Warming Potential
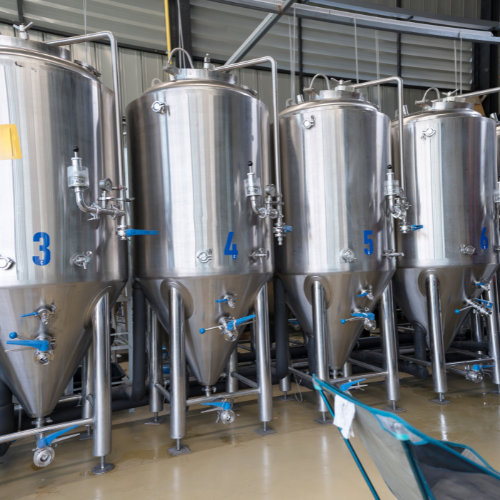
Decarbonizing Food Processes with Industrial Heat Pumps
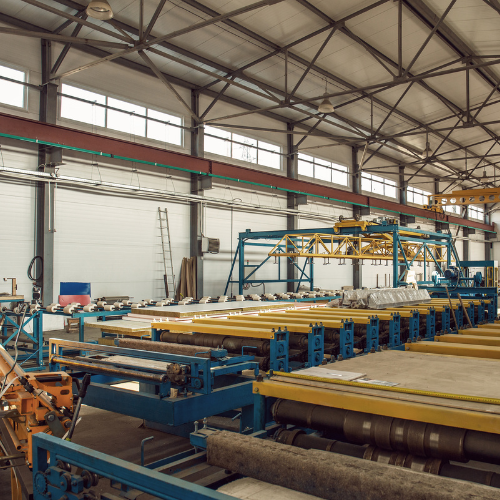
Interconnected Efficiency: Leveraging Ammonia Heat Pumps for Sustainable Manufacturing
STAY UP TO DATE
Get the latest industry insights and important updates delivered right to your inbox.
|